Researchers at the R&D Center for Lubricating and Protecting Materials, Lanzhou Institute of Chemical Physics, Chinese Academy of Sciences, have found that Ni3Al matrix high temperature self-lubricating composites with coarse particle show lower friction coefficient and wear rate.
They first fabricated the Ni3Al matrix high temperature self-lubricating composites with different particle size by the powder metallurgy technique then and investigated the effect of particle size on the mechanical and tribological properties of the composites.
The results showed that the coarse particle composite exhibited the lowest friction coefficient and wear rate compared to the fine particle ones at a wide temperature range from room temperature to 1000℃. The reason for the low wear rate was that the coarse bulk phase could provide better deformation resistance and higher load bearing capacity than the fine microstructure.
The composite fabricated via powder metallurgy technique has many advantages, such as composition precise controlling and also easy to realize a special function property. The sintering process and variables involved in sintering, such as temperature, time, atmosphere, pressure, heating rate and cooling rate, as well as variables related to raw materials including the size of powder particles, shape and agglomeration of particles, had been studied extensively.
The effect of particle or grain size on the tribological behavior of materials is an important topic that has received much attention. In general, finer size materials have better wear resistance owing to the improved mechanical properties. But there have been few reports, where the opposite is found. The reason is that larger particles carried greater load, as well as protected other smaller particles from being gouged out during the wear process.
The work has received support from the National Natural Science Foundation of China (NSFC), the Innovation Group Foundation from NSFC and the National Program on Key Basic Research Project of China.
The findings have been published in Tribology International (Tribology International 44 (2011) 1800–1809).
Tribology International Paper
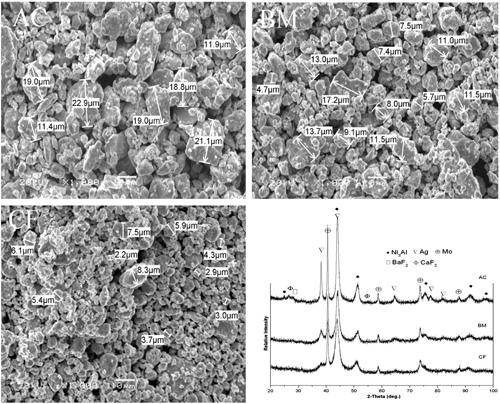
SEM morphology of the milled powders and XRD results of the milled powders: AC, BM and CF